The Dillman Bridge in Meaghers Grant, Nova scotia has been decommissioned for over two years, after a vehicle accident on the bridge deemed the bridge unusable – forcing locals to take a 17-minute detour to get around. However, the concrete and steel structure was also unable to survive the harsh weather that the Maritimes bring, just like many bridges around the area. The bridge is located in the one of the highest exposed and embedded corrosion zones in Canada.
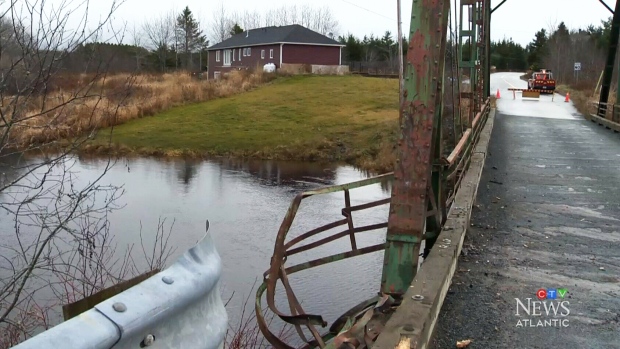
The original Dillman Bridge, a concrete and steel bridge. Image courtesy of CTV News Atlantic
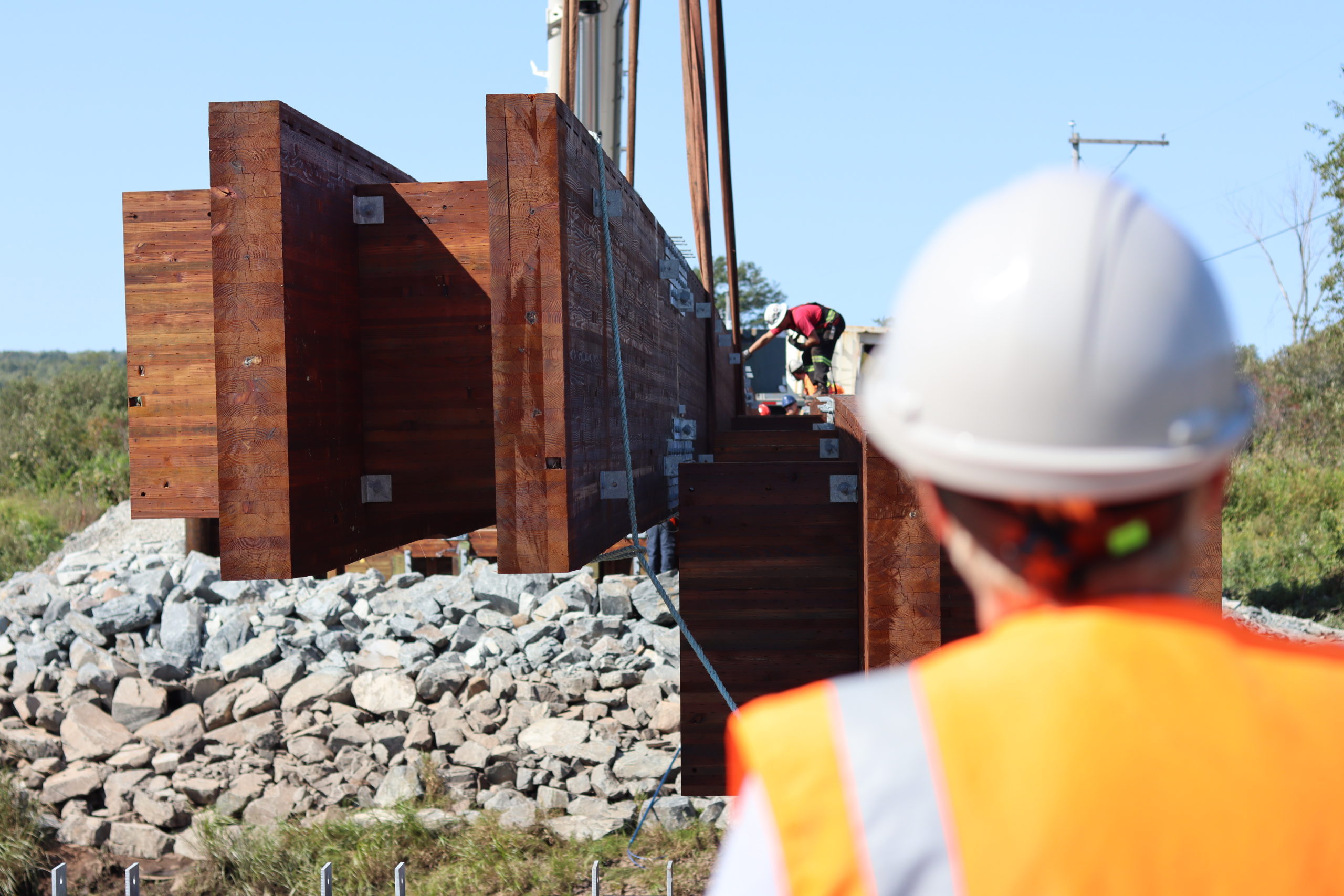
Beams being lifted into place
The province put out a tender for bridge replacement and made the tender available for all products including timber. Timber Restoration Services (TRS) along with Wood Research and Development (WRD) were awarded the tender for both supply/design and install. The timber structure is 35m long by 7.6m wide and is designed for a load rating of CL-625. It has a TL-4 crash proof rail system and an Alaskan yellow cedar handrail. The substructure consists of driven timber piles with a glulam timber back wall specifically designed for timber bridges. The superstructure is comprised of glulam laminated deck panels sitting on eight glulam girders which have two fixed end-moment connections that were assembled on-site. The use of High Strength Fiber (FiRP®) and advanced techniques make this light-weight option not only a cheaper alternative to that of its competitors, but it also provides additional longevity.
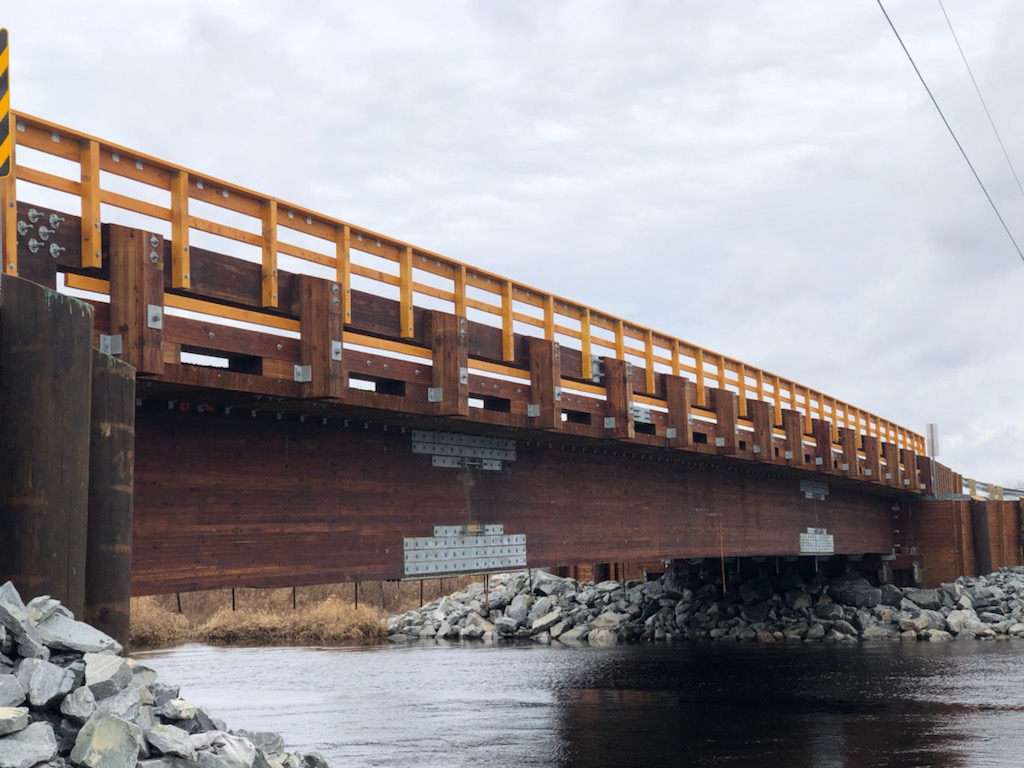
Stunning Alaskan Yellow Cedar handrails compliments the beauty of this timber bridge.
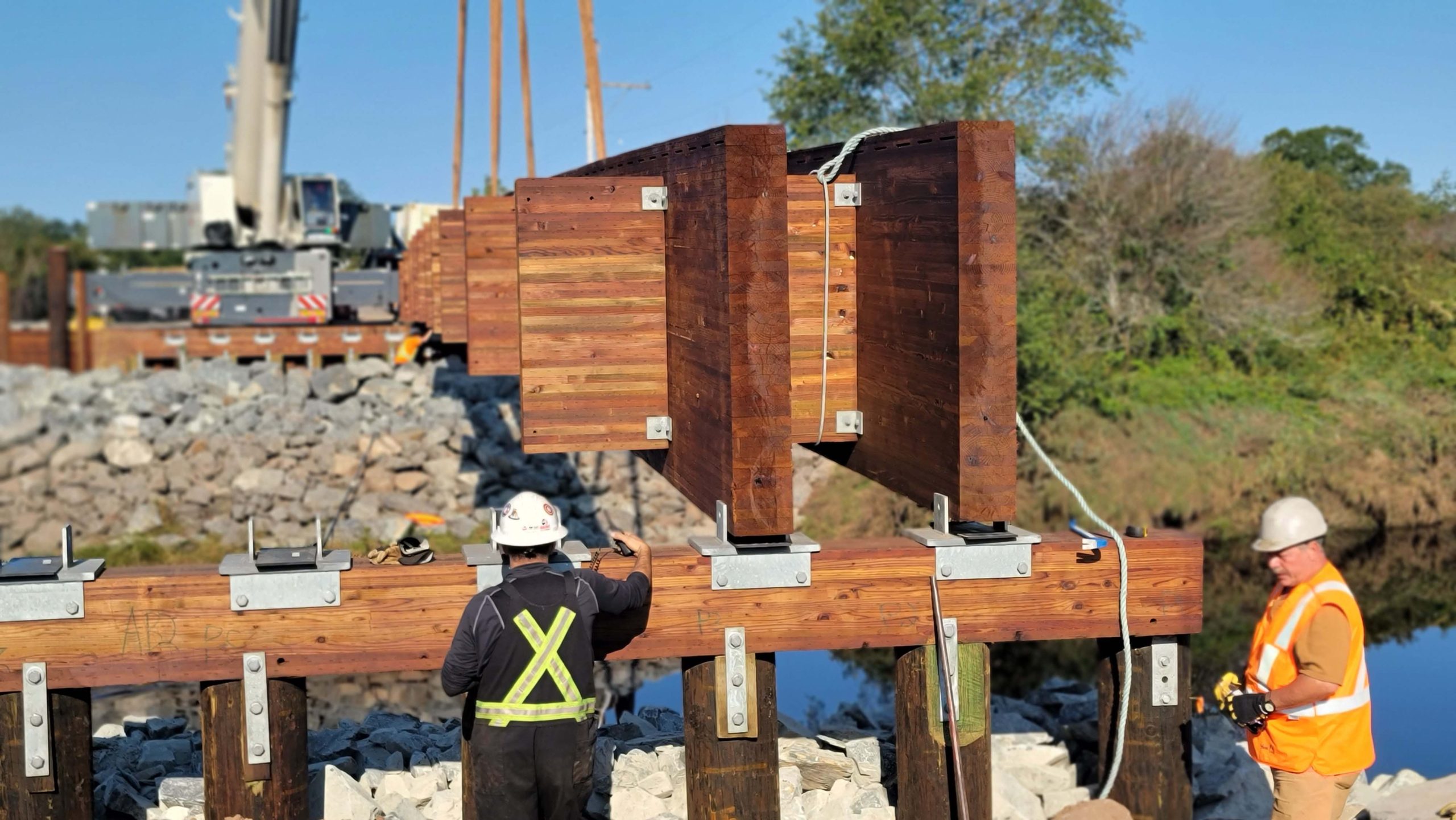
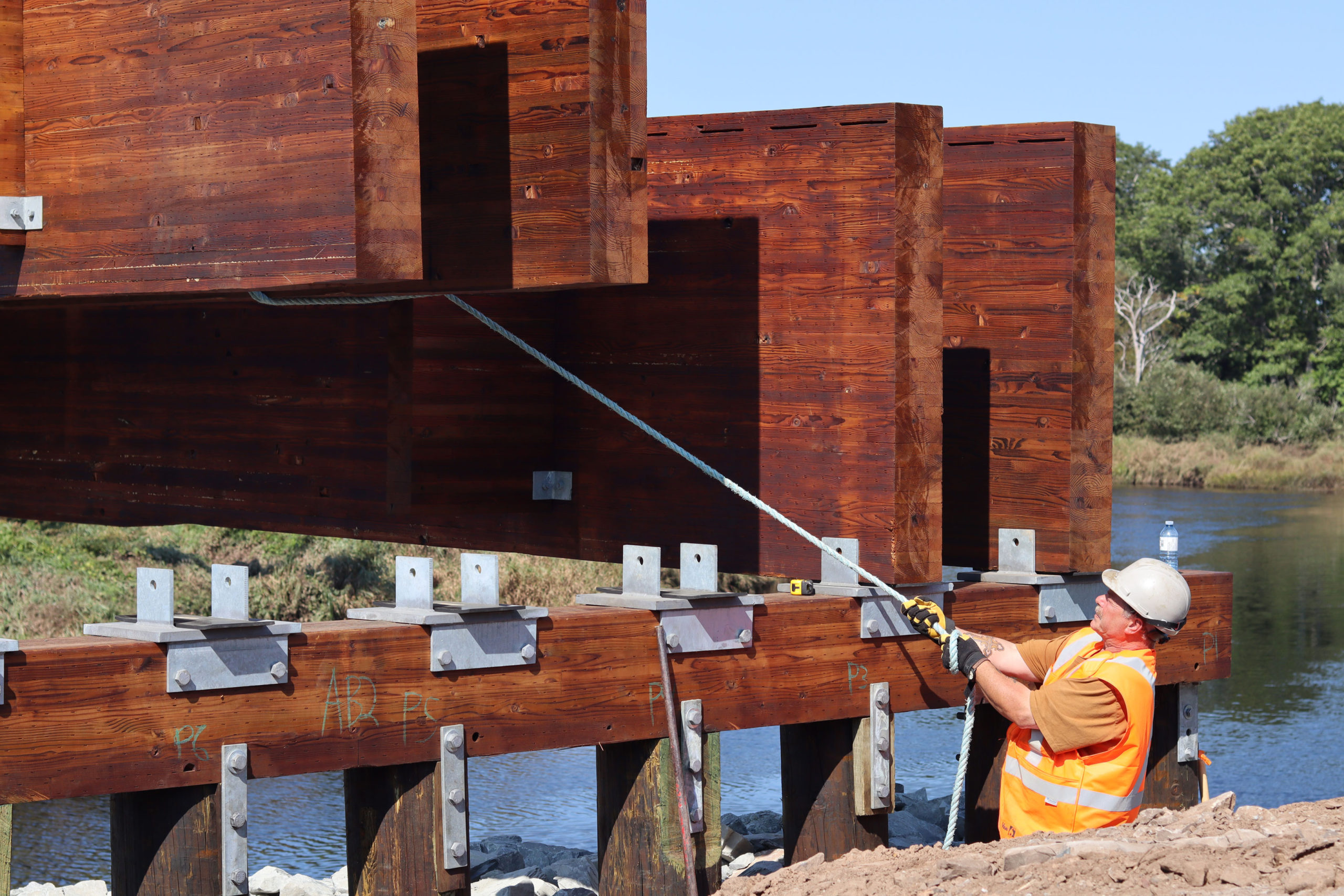
Manufactured off-site for the best results.
Prior to the timber arriving to site, it was manufactured and assembled in our state-of-the-art manufacturing facility prior to treatment. This allows treatment uptake to take place in all through bolt fastener holes, as well as pre-drilled lag holes. Timber inletting is done on edges to prevent bright wood from being exposed, in the event a field fit is required.
All fasteners where possible, are horizontal or vertically from underneath to help with moisture penetration into the bright wood. The structure is then disassembled and sent away for pressure treatment with an oil-based product. The hardware and fasteners are then sent away for galvanization. This method not only is best for extending longevity of the structure but it also allows for an accelerated schedule during install on site.
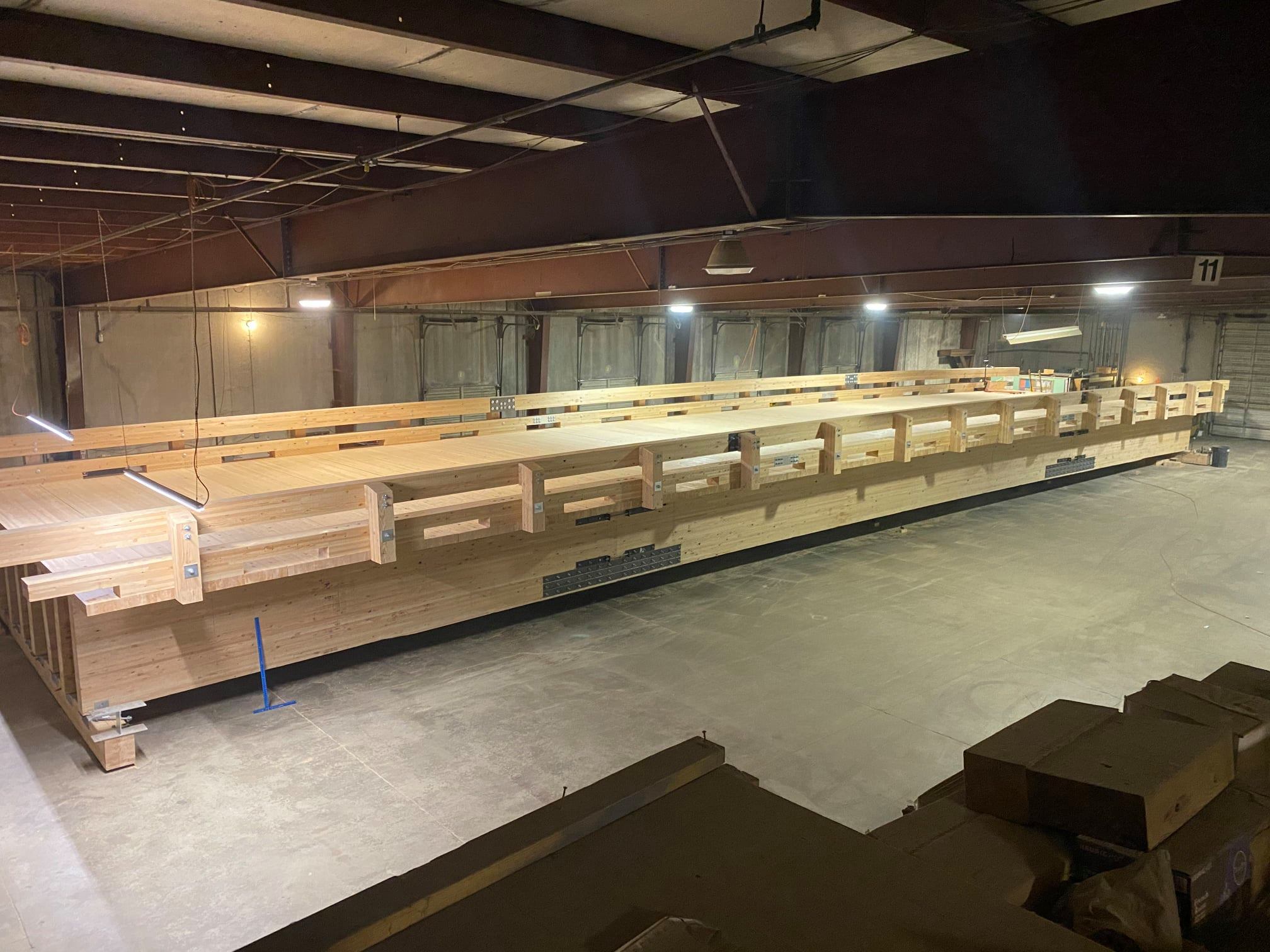
The Dillman Bridge fully assembled in our plant in Jefferson, Oregon.
Timber bridges have many benefits:
Carbon friendly:
Timber Bridges sequester carbon to help with global warming. Timber is 15 to 16 times more carbon friendly then reinforced concrete and 21 times more carbon friendly than steel.
Reduced environmental impact:
Timber’s light weight structure provides many cost benefits as well as a reduced environmental impact. The superstructure does not require a robust substructure that would typically see if it was built from other materials at this span. This means smaller equipment needed as well as a smaller construction footprint.
Reduced costs:
This bridge like many other greater then 18m in length came in at a reduced cost 40% lower than its competitors concrete and steel.
Accelerated construction schedule:
Preassembly of the structure as well as material being lighter weight allows the construction schedule to be greatly reduced, allowing detours and community disruption to be minimized.
Longevity:
A new timber bridge structure is good for 100 years using proper design and installation techniques. A timber structure will far outlast a concrete and steel structure, especially when the location is in a high-risk of embedded and exposed corrosion zones.
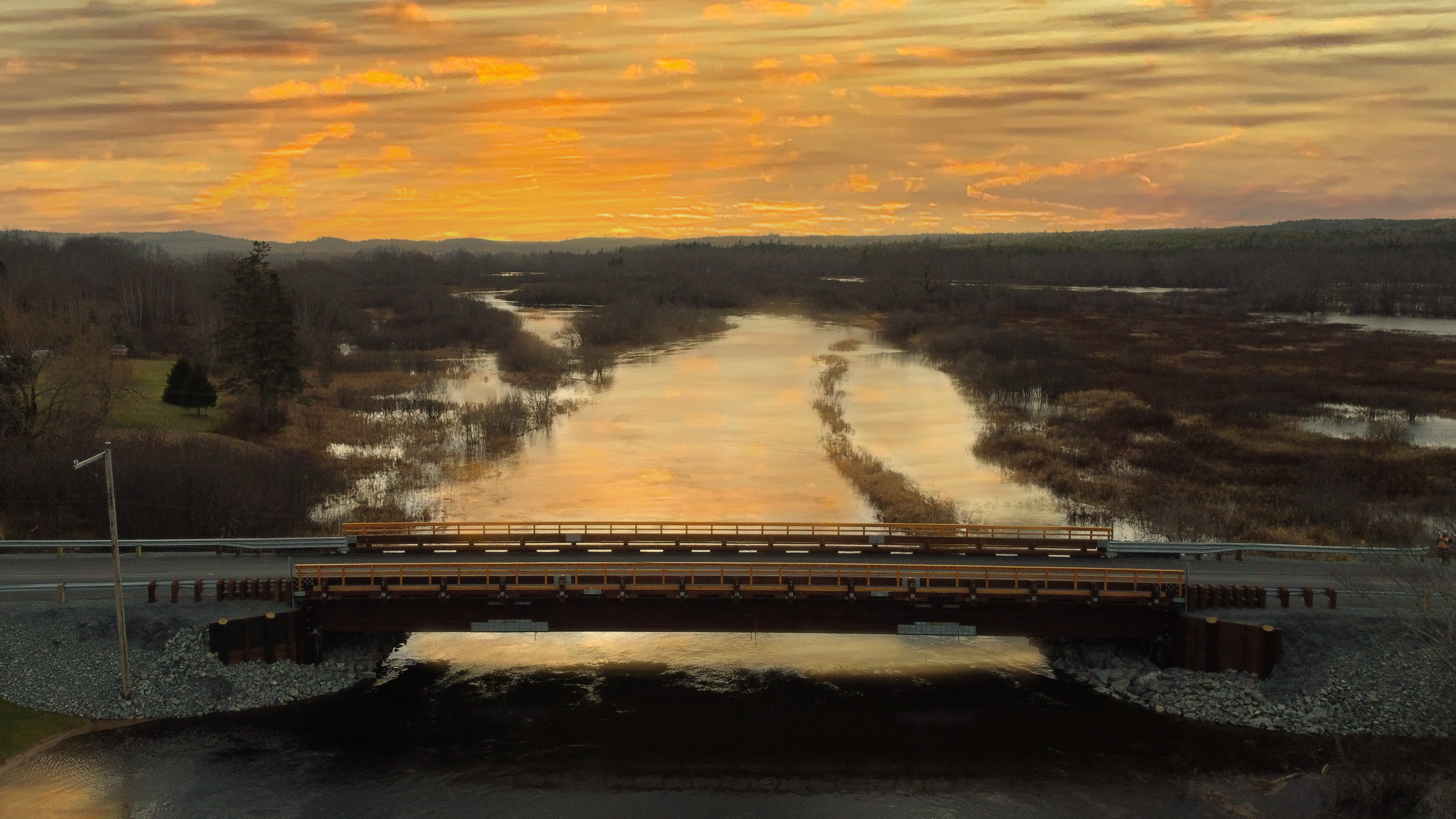
The Dillman Bridge, in its completed state – complete with an amazing backdrop.